amc Fully automated single-wafer processing
Fully automated amc wafer processing equipment
Customer specific processes fit for future
Especially in microsystems technology the requirements to production processes and product quality, as well as cost pressure in wafer processing are high. That´s where amcoss with its wafer processing equipment comes in: we focus on our customers´ needs and on attractive cost-performance calculation. Therefore, every tool may be optimized either for flexible single processes or high throughput. Besides, ams PILOT software independently controls processes in every equipment and therefore supports the operator and optimizes all processes. So, with our equipment you will receive solutions for substrate coating, developing, cleaning, heating/cooling and lift-off, that contribute to reaching your goals.
Choosing the appropriate production equipment is a highly influential aspect of sustainability for a company and their products. With the acquisition of an amcoss equipment you not only opt for an intelligent technical solution, but for more efficiency in various respects.
Process efficiency
Cost efficiency
Protection of ressources and energy efficiency
Ergonomics and safety
Machine types
Modular, flexible, individual – amc machine series
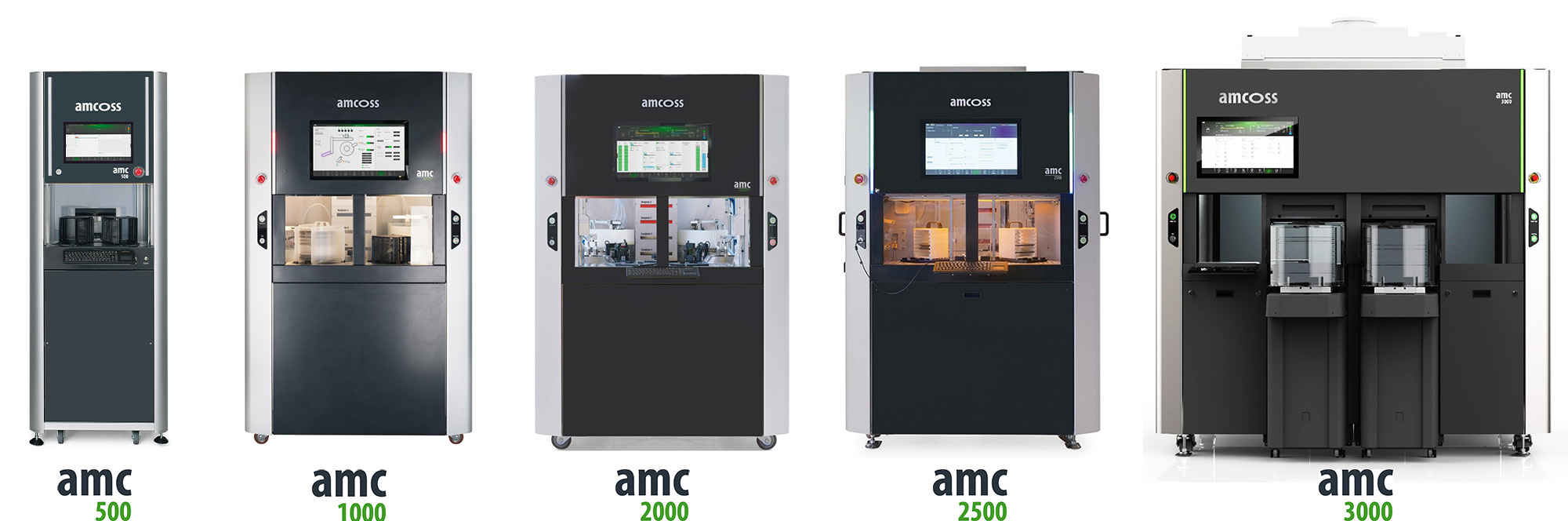
All 5 amc models have been designed as adaptable platforms, so that individual configurations, process solutions and combinations are standard with amcoss. The footprints, however, are very compact and room saving. With, e.g. amc 1000 you will find 3 processes, 1 wafer-handling-station and up to 4 I/O stations on about 1 m² and you may flexibly process wafer sizes between 2“ and 8“.
amc 500 — our mini tool for innovative wet processes
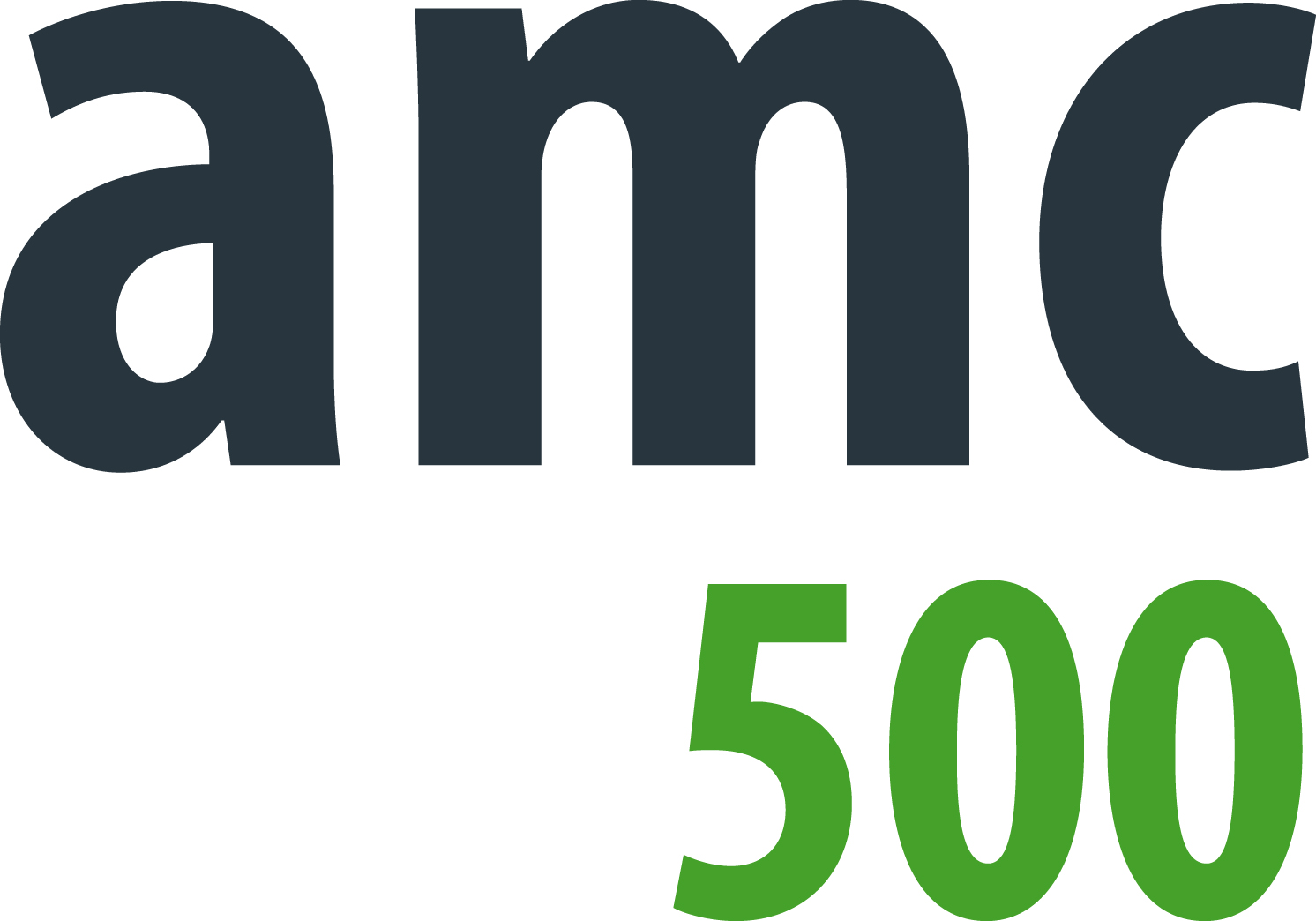
This extremely compact tool for wet processes enables you to make the most of your expensive cleanroom space:
- Wafer diameters: 2” up to 300 mm or up to 9 x 9”
- Up to 2 I/O stations for 2” to 200 mm open cassettes or 300 mm FOUP
- Max. 3 integrated individual chemical supply systems (more possible in external media unit)
- 1 two-link robot handler with single end effector for low contact handling
- Outer dimensions W x L: 740 x 1360 mm
- A separate enclosure of the process area made of resistant material extends the safety features.
amc 1000 — our transitional model to fully automatic low-scale production
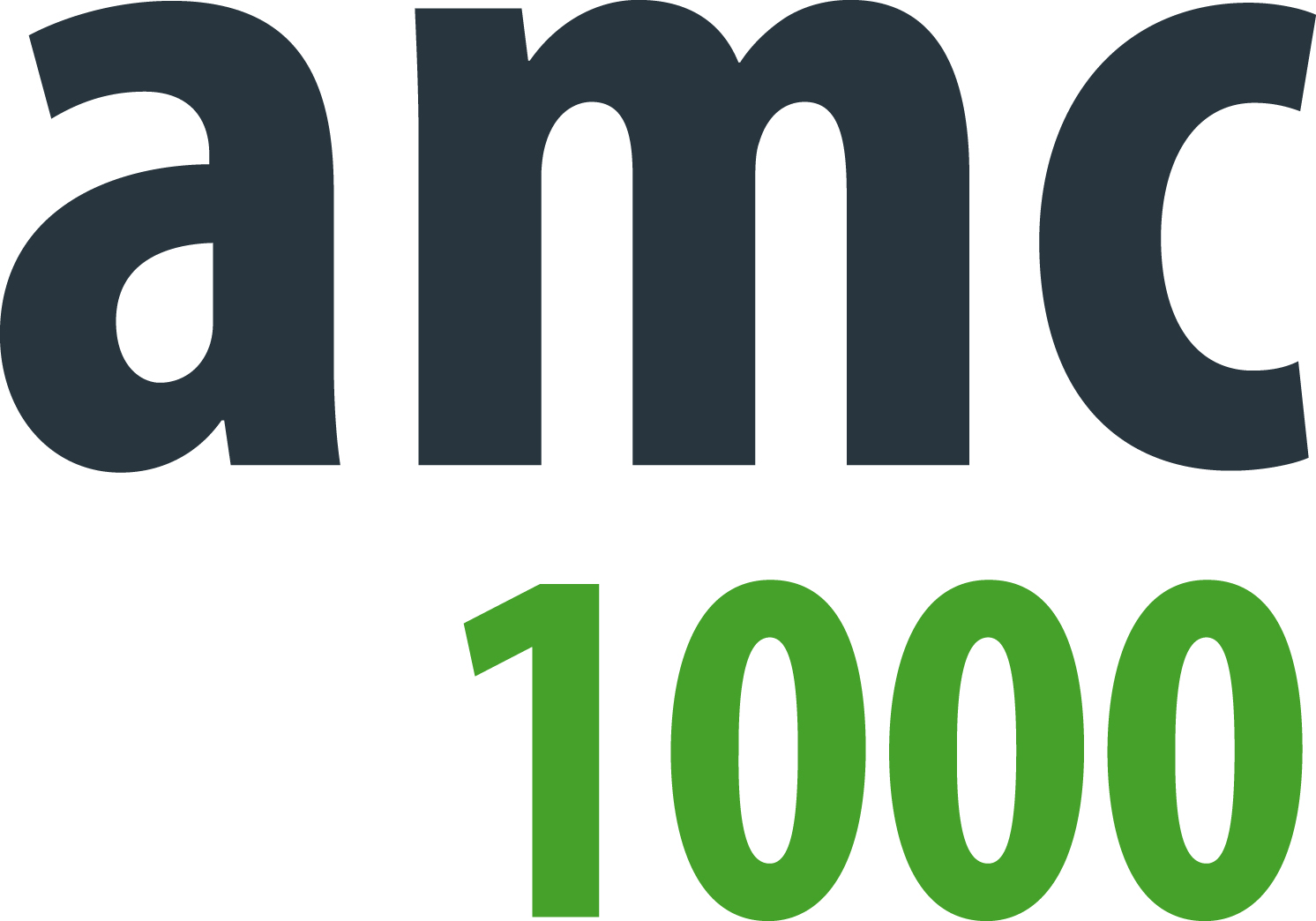
Flexible machine configuration and processing of different wafer sizes:
- Wafer diameters: 2“ to 8“
- Up to 4 I/O stations for 2“ to 6“ (max. 4x open carriers or 2x SMIF) or
- Up to 2 I/O stations for 8“ (open carriers or SMIF)
- Max. 3 individually selectable process modules
- 1 two-link wafer handler
- Outer dimension W x L: 1236 mm x 1150 mm
amc 2000 — our workhorse, designed for flexible use or very high throughput
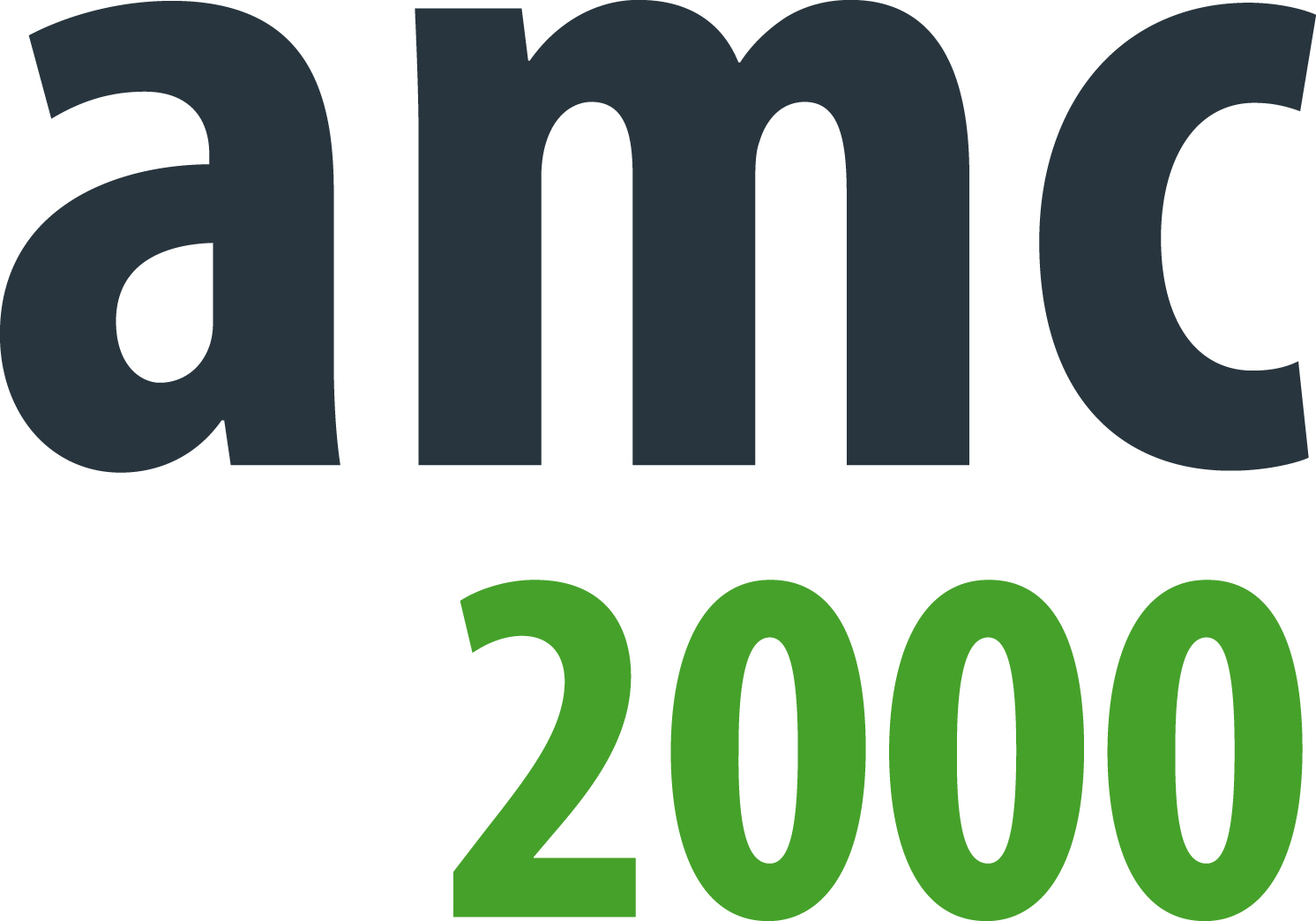
Highly flexible machine configuration and processing of different wafer sizes:
- Wafer diameters: 2“ to 8“
- Up to 4 I/O stations for substrates 2“ to 8“ (max. 4x open carriers or 2x SMIF) or
- Max. 5 individually selectable process modules
- 1 two-link wafer handler
- Outer dimension W x L: 1382 mm x 1596 mm
amc 2500 — our all-rounder for multiple processes & substrates
Compact service package for high throughput:
- Wafer diameter: 2“ bis 8“
- According to configuration of wafer handling up to 4 I/O-stations (max. 4 x open carriers or 3 x SMIF)
- Max. 7 individually selectable process modules
- 2 two-link wafer handlers or
- 1 two-link wafer handler on linear track
- Outer dimension: W x L: 1414 mm x 2048 mm
amc 3000 — established quality for a wide range of applications up to 300 mm
Offers the possibility of FOUP loading via robot or rail system, as well as the integration of an optional 300 mm SECS:
- Wafer diameters: 150 mm to 300 mm or 7 x 7” to 9 x 9”
- Up to 2 I/O stations for 150 mm to 200 mm open cassettes or 300 mm FOUP
- Max. 5 individually selectable processing modules
- 1 two link robot handler with single or double end effector
- Outer dimensions W x L: 2082 mm x 2003 mm
Highlights
Added value through perfected technical details
Substrate variety
Substrate variety
Every amc equipment is a genuine Bridgetool, which means that different substrate sizes may be processed simultaneously. When changing wafer size, no technical adjustments and retrofits are necessary. So, utmost flexibility is guaranteed. With the help of laser sensors our intelligent carrier scanner identifies substrate size, carrier type, substrate bow and thickness, mixed or double loaded slots and wafer protrusion.
Substrate range
Thin
80 µm 6“, bow concave / convex
150 µm 8“, bow concave / convex
Thick
15 mm 6“, weight 0,75 kg
Shape
round 2” – 12”
square, rectangular, up to 8” x 8”
Materials
Si, SiC, GaN, GaAs, sapphire, glass, etc.
Genuine Through-the-wall installation
Genuine Through-the-wall installation
Because the process chamber has been realized as a HTU with particle filter, which ensures a fully climatized process atmosphere (temperature, humidity) a genuine through-the-wall installation with all its advantages is possible.
Easy access to all components
Easy access to all components
All doors and the windows on the sides and the back of the equipment can be easily removed and put aside space-savingly. Especially the frameless side windows are very lightweight. So, comfortable access to all modules and controls during machine conversion and maintenance is guaranteed.
Unique machine design
Unique machine design
During development of the classy design by an industrial designer our focus was not only on modern appearance, but especially on user-friendliness, functionality and ergonomics: the large windows allow good insight and access to the machine, all operating elements are in favourable positions and both integrated LED status lights can be seen well from any direction. The anthrazite coloured surface coating is on the one hand insensitive towards chemical cleaning agents and on the other hand absorbs the amber light in the cleanroom which is relaxing on the eye.
Reduction of controls
Reduction of controls
Due to intelligent designs, advantageous machine layout, and the use of standardized industrial components, the number of control parts as well as other components could be substantially reduced. As a result, error rate decreases, material costs can be saved, service is being facilitated, and costs as well as labor input are reduced in general.
Flexible machine adjustments
Flexible machine adjustments
Its modular setup and adaptable software ensure that the amc equipment can be easily adjusted or extended directly at the customers’ site. Also, if the machine is not fully equipped with process modules, the installation of another process module can be simply realized by means of an integrated conversion mechanism. Hot- and coolplates may be added. So, whenever their process requirements change, our customers can be offered uncomplicated solutions.
Easy maintenance
Easy maintenance
The whole electronic system can be easily accessed at the back of machine. It has been placed above the media system and is therefore totally separated from it. Use of long-living, proven standard components, easy installation and removal of bowls as well as hotplates, and many other of the already mentioned highlights make maintenance simpler and reduce its requirements, as well as machine downtime. In addition, the whole system is being supported by the comfortable service functions of ams PILOT software.
Unique operating concept
Unique operating concept
ams pilot control software as well as the overall equipment layout have been designed to offer best possible user-friendliness, ergonomics and comfortable handling. Our modern software can be intuitively operated and supports even unexperienced users. Furthermore, operating- and service personnel will be able to comfortably and safely handle all machine units.