Wafer Coating
Perfect, uniform coating layers
Linear, triaxial positioning arm
Linear, triaxial positioning arm
All desired positions of the dispense nozzle above the substrate are freely programmable on the X, Y or Z axes with the help of our integrated servo control. This enables an absolutely accurate nozzle positioning and, furthermore, dispensing in a spiral or meandering movement. Calibrations or test-runs become unnecessary, but uniformity and resists savings increase enormously.
Innovative single nozzle gripper
Innovative single nozzle gripper
The positioning arm only carries 1 spray nozzle at the time which holds two decisive advantages: Firstly, there will be no particle build-up due to friction of materials, for only one tube is being moved. Secondly, all nozzles not needed at the moment remain in the nozzle storage with rinse and dripping pan which prevents the nozzle tips from going dry and avoids any undesired dripping onto the substrate.
RFID chuck-identification
RFID chuck-identification
Through automatic chuck-identification the system will always recognize which chuck is being used at the moment and will so exactly adjust maximum rotation speed and eventual acceleration. Not only user security is being increased drastically, but also processing flexibility for a great variety of substrates on different chucks.
EBRsquare for square substrates
EBRsquare for square substrates
With the help of our special and singular EBR system, edge bead removal for square substrates or wafer flats may be started directly within the coater bowl as soon as the coating process has been finished. Wafers do not have to be removed or repositioned. EBR may be programmed using absolute distance values.
Air barrier plate
Air barrier plate
An optional air barrier plate forestalls the formation of edge beads on angular substrates. Moreover, high-viscosity resists can be processed better, and thick layers of coating may be applied easier. All of this helps to improve homogeneity of the coating layer. Process results are being optimized and rejects minimized at the same time.
Puddle- und spray coating in one bowl
Puddle- und spray coating in one bowl
Because all the dispense arms of our equipment are being linearly moved, puddle and spray coating are possible within the same bowl and make a separate spray coating station unnecessary. A fact that saves machine space and time and increases flexibility of applications. Moreover, not having to use a pneumatic system also saves energy.
Other important features
- All axles are linearly driven motor axles. In contrast to pneumatic axles, those can be positioned more precisely and programmed via software.
- EBR is also possible on a separate arm instead of on the dispense arm. This improves flexibility as well as the results of the coating process.
- The process bowl instead of the chuck rises and lowers when handling substrates in or out. This helps to stabilize the chuck drive considerably and it also enables highly dynamic functions.
- A variety of resist pumps to choose from: we can offer amcoss´ economic and innovative dispense systems such as motor driven syringe and trap tanks, but also every other resist pump that is available in the market.
- Due to our linearly driven motors up to 6 resists, EBR and pre-wet nozzle are possible within the same bowl.
- Our elaborate bowl design helps to avoid cotton candy when processing high viscosity resists and so guarantees optimum process results.
- Programmable rinse for wafer backside as well as coater bowl.
- Optional mini environment: the whole equipment or just parts of it can be temperature controlled. Therefore, comprehensive temperature and humidity control is possible.
- Contact-free wafer centering „on-the-move“, centering for square substrates or fully automated pre-aligment may be selected.
- Media temperature control through hose-hose temperature control is possible.
Coating processes
- Positive- & negative coating
- SU8 coating
- PMMA coating
- Spray coating
- Thick-resist coating
Wafer Developing
Great variety of applications, best results
Special bowl rinse
Special bowl rinse
The process bowl is being cleaned with a novel rinse system. So, cristal- or particle buildup with the risk of wafer contamination is being avoided and the reject rate can be diminished.
DIW and media temperature control
DIW and media temperature control
Besides our standard hose-hose media temperature control system, DI water may also be temperature controlled. A fact that helps to optimize process cycles and their results.
Megasonic-supported developing
Megasonic-supported developing
Our optional megasonic-support has the advantage of faster media change on the substrate which helps to make development of deep structures, e.g. SU8, possible.
RFID chuck identification
RFID chuck identification
With our automtic chuck identificaction, the system will always recognize which chuck is being used at the moment and will so exactly adjust maximum rotation speed and eventual acceleration. For the user not only security is rising considerably, but also the flexibility in the processing of a wide range of substrates on a variety of chucks.
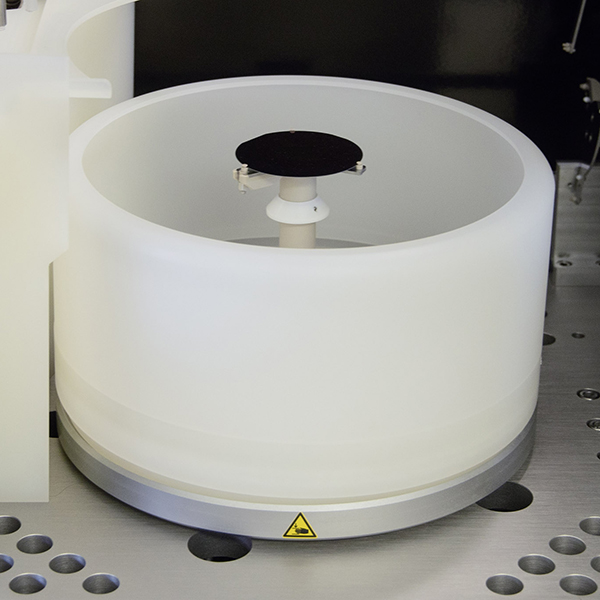
Bowl lowering
Bowl lowering
Within the amcoss system the process bowl instead of the chuck is being lowered when depositing or withdrawing a wafer. So, chuck drive remains stable and highly dynamic functions become possible. While the bowl is in lowered position the chuck is a little higher than the bowl rim which makes manual deposition of the substrate on the chuck within our semi-automatic amr equipment simple and more comfortable .
Puddle and spray developing in one process bowl
Puddle and spray developing in one process bowl
Because the developer arm is linearly driven, puddle and spray development within one bowl become possible and there is no need for a separate spray development station. This saves machine space and time and increases application flexibility. Without a pneumatic system you also save energy.
Additional important features
- All movement axes are linearly driven motor axes. In contrast to pneumatic axes they may be positioned with greater precision and programmed via our software.
- Up to 5 developer media within one bowl are possible.
- Programmable surface and backside rinse of wafers.
- Servo-controlled nozzle positioning which can be programmed with absolute distance values in the ams pilot software.
- Optional temperature and humidity control
Developing Processes
- Puddle developing
- Spray developing,
- Developing with TMAH, KOH & Solvents
Wafer Lift-Off
Safe, effective, and user-friendly
Reduced media temperature
Reduced media temperature
DMSO Megasonic can be used at significantly lower temperatures (50°C), which results in shorter processing time and higher throughput. Moreover, it saves energy.
Protecting structures by not using high pressure
Protecting structures by not using high pressure
Megasonic Lift-off works without high pressure during media dispense. So, this is a very gentle process and sensitive substrates and structures can be worked on without risking damage or breaking. Reject and costs are being reduced.
Increased security
Increased security
Traditional Lift-off media have to be applied at temperatures close to their flashpoint, which constitutes an enormous safety risk. With megasonic lift-off media are being used at relatively low temperatures. So, the danger of inflammation does not exist and the whole process is safe for both man and machine.
Health protection
Health protection
With megasonic lift-off there is NO atomized spray which could affect the operators´ health at opening the machine. Also, cleaning, filtration, and assembly of the equipment in general, are being facilitated.
Variety of substrates without conversion
Variety of substrates without conversion
Our megasonic system is able to process any size and form of substrate as well as any substrate material by only choosing the correct chuck, but without any conversion.
Additional important features
- High- or middle-pressure cleaning with DIW or solvents
- Special reclaim solution for very low media consumption
- Easy recycling of the lifted metals
- Programmable wafer backside, topside and bowl rinse
Lift-off processes
- Standard metal lift-off with solvents like DMSO
- Protecting metal lift-off with DMSO megasonic
- Solvent strip
Wafer Cleaning
Flexible combinations for manifold cleaning processes & substrate types
Select between wet-in/dry-out and dry-in/dry-out
Select between wet-in/dry-out and dry-in/dry-out
Dry-in/dry-out, as well as, wet-in/dry-out cleaning by spraying the substrate within the carrier are offered as standard, which enables optimized processes.
Various processes on a very compact platform
Various processes on a very compact platform
Even on our smallest amc 1000+ equipment with a footprint of only just about 1 sqm, a frontside, backside and an Edge Bevel cleaning module may be installed, with all three processes running automatically at the same time. Furthermore, frontside and backside cleaning may be integrated within the same module, so as to save additional machine space.
Great variety of cleaning media and processes
Great variety of cleaning media and processes
Different cleaning media that are compatible with each other may be used within the same bowl. Moreover, differing cleaning methods may be combined flexibly in various process modules within one equipment. We are, however, able to realize all established cleaning processes. You will need less machines and therefore save cleanroom space.
Other important features
Cleaning with:
- Brush
- High pressure
- Megasonic
- Binary spray
- Mixing nozzles
- Spray nozzles with N2 support
- All established cleaning media are possible
Cleaning Processes
- Post CMP cleaning
- RCA cleaning
- Frontside, backside and edge bevel cleaning
- TSV cleaning
Wafer Etching
Various etching processes are standard
Etching of wafers & masks
Etching of wafers & masks
Various etching processes of a multitude of round and square wafers and masks are available as standard solutions.
Precise chemicals–temperature control
Precise chemicals–temperature control
Our new, unique solution for precise media temperature control eliminates the need for pre-dispense before etching. Inadvertent mixing of chemicals almost becomes impossible.
Novel chrome etchant recycling
Novel chrome etchant recycling
amcoss GmbH and FIMA-Chem GmbH have jointly developed a turnkey solution for chrome etching. While FIMA-Chem supplies the spiking chemicals, amcoss has engineered and integrated the appropriate hardware into the amc tools. This represents a perfect cooperation of two innovative companies supporting our sustainability concept, environment protection and reduction of costs.
Using a novel technique, we can recycle the etchant on the tool which can then directly be re-used to process another substrate. Highly concentrated additives are employed to replenish the used-up etchant thus preparing it for another run. So, the etching chemical is used at maximum efficiency, saving a significant amount of etchant costs.
Benefits
- Significant decrease of processing costs
- Vastly reduced impact on the environment due to reduced use of chemicals and less waste
Etching processes
- FEOL etching
- BEOL etching
- Metal etching
Wafer Heating/cooling
For adjustable tempering of substrates
Great and flexible number of hotplates
Great and flexible number of hotplates
Up to 5 hot- or coolplates are possible for one temperature module. In all amc models every process module can be exchanged for a hotplate stack, so as to transform the equipment into a mere tempering tool.
Our semi-automatic amr tools can be complemented with separate hotplate modules in different sizes.
Especially comfortable access to plates
Especially comfortable access to plates
Due to our well-thought-out equipment design, access to the hotplates for maintenance from the back or the side of the machine is easy and comfortable, no matter where the stack is placed within the machine. Furthermore, the plates may be easily removed or fitted into free stacks.
Adjustable standard hotplate
Adjustable standard hotplate
Our standard hotplate with a temperature range from 60 to 200°C may be adjusted to the following settings (in reference to a 200 mm wafer):
- +/- 0.1 K uniformity
- +/- 0.5 K <= 100°C
- +/- 1 % >100 °C
Other important features
- High-temperature hotplate (60 – 450 °C)
- HMDS vapor priming hotplate (60 – 200 °C)
- Single- or multizone-hotplates
- Coolplate (10 – 60 °C), with either water- or passive cooling
- Curing with UV-light or supported by UV-light
- Distance control to hotplate surface via fixed proximity, programmable proximity, vacuum contact
- Cover heating
Wafer-handling
The perfect wafer-handler for every demand
Selection of adequate end-effectors
Selection of adequate end-effectors
For wafer handling it is important to choose and adjust the most adequate end-effector for the wafer type to be processed. We are highly experienced in this field because we do not only offer a great variety of end-effector types for our amc processes, but also the engineering of end-effectors for equipment of other manufacturers.
Proven „pick&place“ 2-link robot
Proven „pick&place“ 2-link robot
amcoss only uses high quality standard wafer handlers for their equipment which have proven successful in use over the years. They are being adjusted to our customers’ needs. This increases reliability and guarantees spare parts at any time.
Intelligent slot-scanning
Intelligent slot-scanning
The intelligent slot-scanner with the aid of laser-sensors identifies the wafer size, carrier type, substrate bowing and thickness, double- or cross-loaded slots, as well as a possible wafer protrusion.
- Automatic End-effector changer possible if different end-effectors are necessary. They will be stored above the wafer carriers and may be used fast and flexibly when needed.
- Any form and weight of substrates may be handled with our end-effectors.
- Linear Track construction within the equipment in order to gain maximum range.
- Slot-Scanning with laser sensors for identification of wafer size, carrier type and double- or cross-loaded slots
- OCR, Bar- and Matrix Code Support
- Automatic Flip-Station for backside-coating
- Handling of perforated wafers
- Contactless wafer centering „on-the-move“, centering for square substrates or fully automated Pre-Alignment may be selected.
Wafer-handling possibilities
- Single end-effectors
- Double end-effectors for higher throughput or for wet-dry applications
- Standard horse shoe vacuum end-effectors
- Low contact vacuum end-effectors
- Edge gripper for wafers (gripping at wafer edge)
- Wet-handling end-effectors available
- Handling of ultrathin wafers